How has vertical farm design changed over the years?
See the progression of the Growcer Osiris vertical farm and the reasons behind the improvements.
We invested research and time in a turnkey modular farm that gets you growing year-round and keeps you growing.
But everyone starts somewhere.
So here’s the progression of the Growcer farm over time.
Switching away from shipping containers
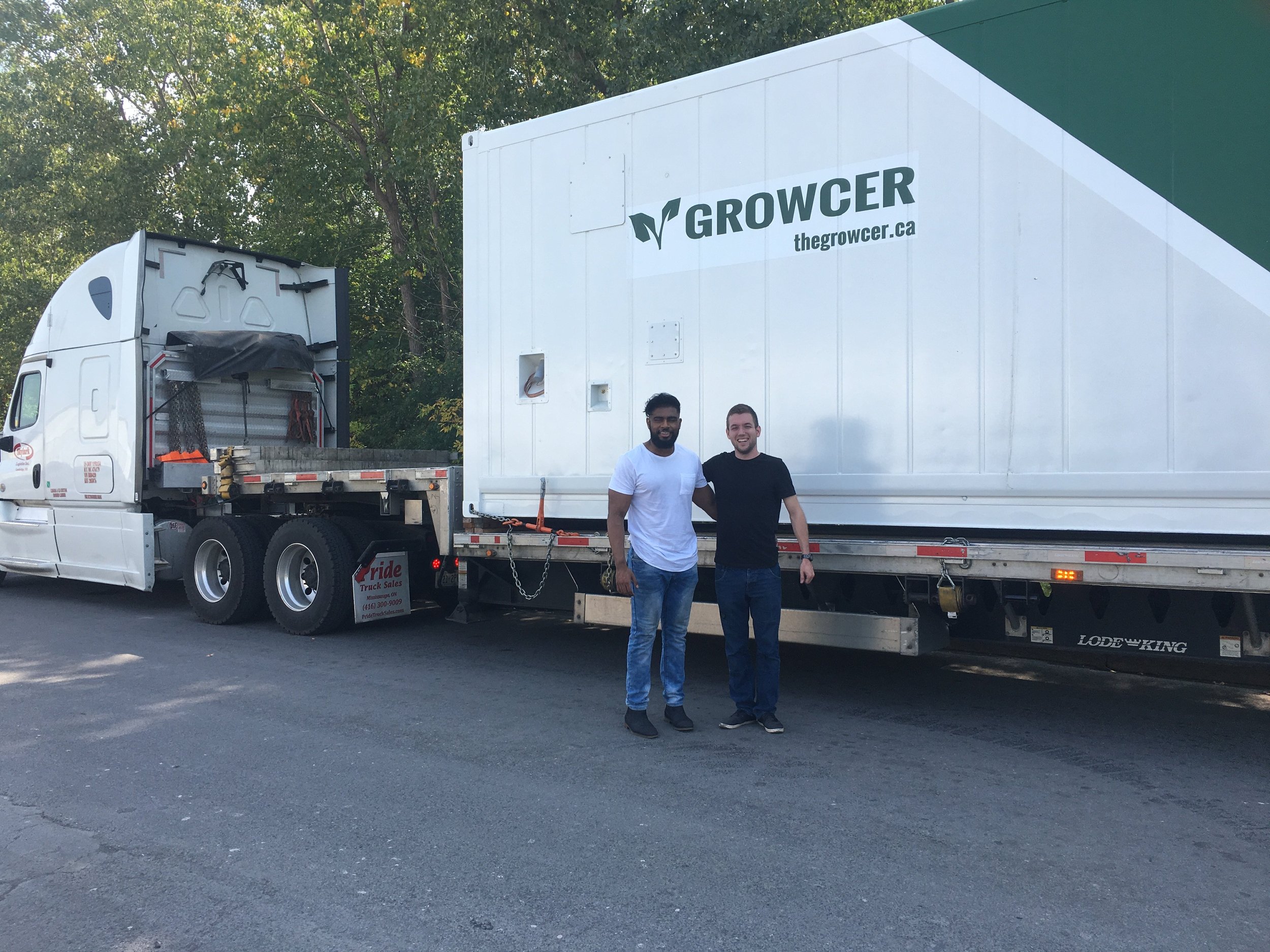
Growcer’s very first farm en route.
Refurbishing shipping containers into container farms is a great way to reuse materials. Upcycling was part of the original design for the Growcer farm, but we quickly realized that there were environmental pitfalls that often outweighed the benefits. Shipping containers are reused for multiple other industries outside of vertical farming, but we discovered that their construction and especially, insulation, wasn’t what was best for yield optimization, plant health, and energy usage.
We wanted to create a better home for plants - and your business - to thrive.

In 2020, we moved our manufacturing to Canada (we’re now 100% designed and built in Canada) and also moved from licensing (buying from a third-party) the farm technology to building our own in-house. We learned a lot in the four years we had spent in vertical farming and wanted to put our insights and research into action and build a Growcer farm that would work sustainably, reliably, and for more people in more places.
We switched from shipping containers to custom-built modular structures because we could:
Increase growing space
Improve insulation (and therefore energy efficiency to keep operating costs reasonable)
Improve temperature control (this is big for plant health and remote communities)
Increase lifespan (up to 30 years instead of 25-years or less for shipping containers)
Increase working aisle space to improve operator experience (more room to move around!)
Design the farm with a slanted roof to reduce the collection of snow or rain water and minimize risk for our customers
The image shows up close what structural insulated panels (SIP) look like.

Switching to a modular structure increases growing (and working) space.
From NFT hydroponics to DWC hydroponics
But first, some definitions:
Nutrient film technique (NFT): plants sit in gutters with a shallow nutrient solution that flows by plant roots. (Growcer’s first farm)
Deep water culture (DWC): plants sit on floating rafts under lights with their roots in a nutrient solution. (Growcer’s current farm)
DWC is more forgiving for those trying to grow plants for the first time at a commercial scale. It also means that in cases where the farm loses power, harvest loss is far less likely because your plant roots are always submerged in water with access to food to grow (no power in an NFT farm = no pumps to deliver water or nutrients!).
In the case of operator days off, well, they are actually possible in a DWC farm!

A DWC system also offers more reliability and temperature stability because roots are always submerged in water.
A DWC system also offers more reliability and temperature stability because roots are always submerged in water.
Disease potential and yields are fairly equal across systems and good maintenance makes a bigger difference on how much yield you can extract from your hydroponic set up in all cases.
Growcer’s vision is to make year-round farming more accessible for all, so we designed our farms with that in mind.
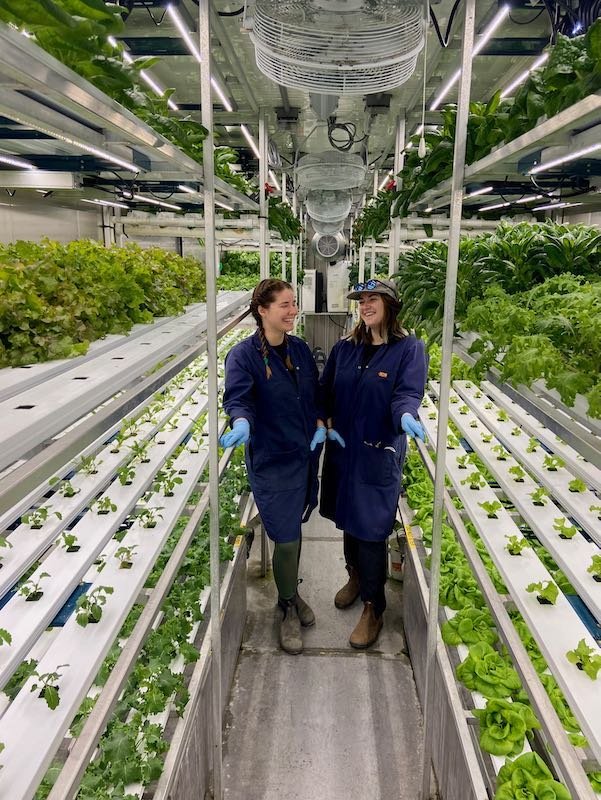

Operators in one of Growcer’s older NFT farms versus inside one of Growcer’s DWC farms.
The bottom line
DWC is the most forgiving system for new growers and considered the most accessible technology when compared to NFT and ebb and flow systems.
Our DWC modular farm was built with the goal of making vertical farming accessible to anyone who wants to grow year-round. We wanted to make the technology less daunting for first time growers, as well as experienced green thumbs. Ultimately, we make systems for people who care about food, regardless of skill level.
Bringing R&D in-house
How can you trust we know what we’re talking about if we don’t show you? In 2018, Growcer created a research and development farm headquartered in Ottawa.
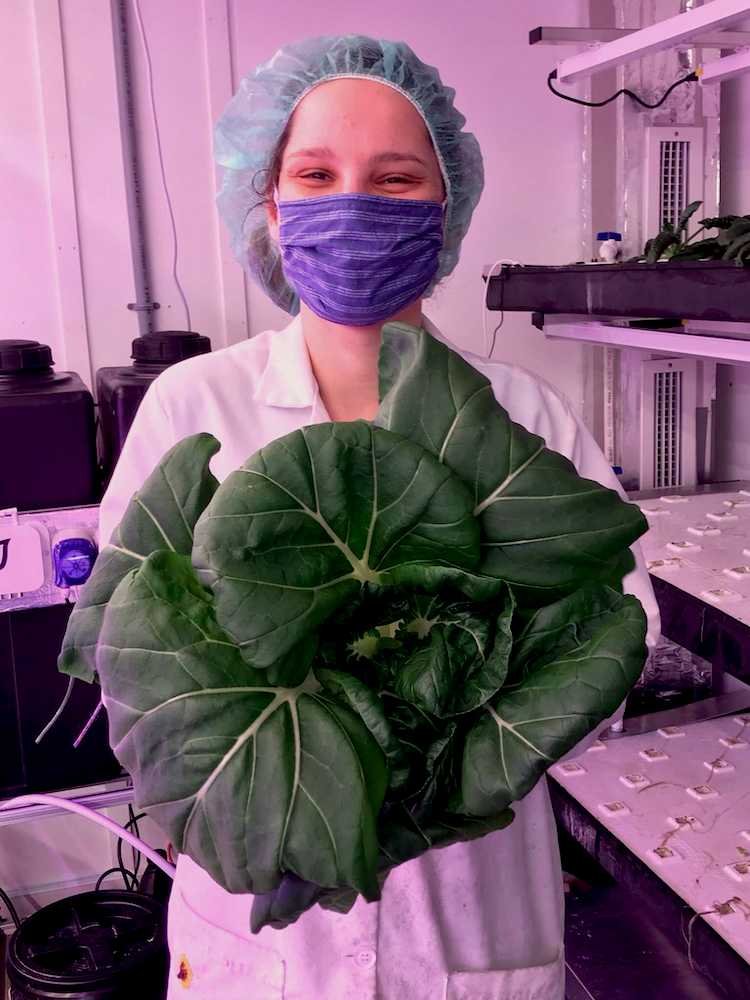
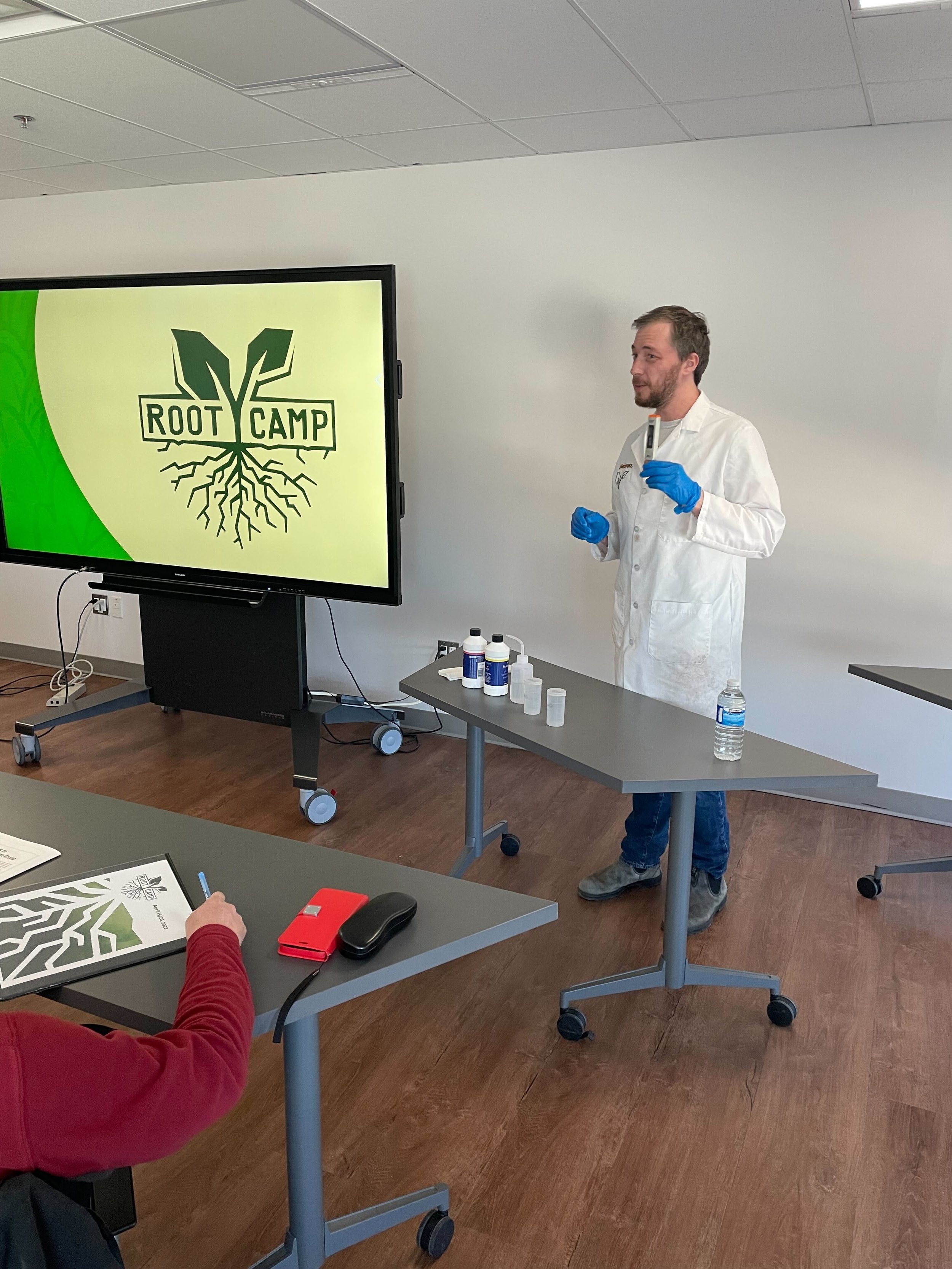
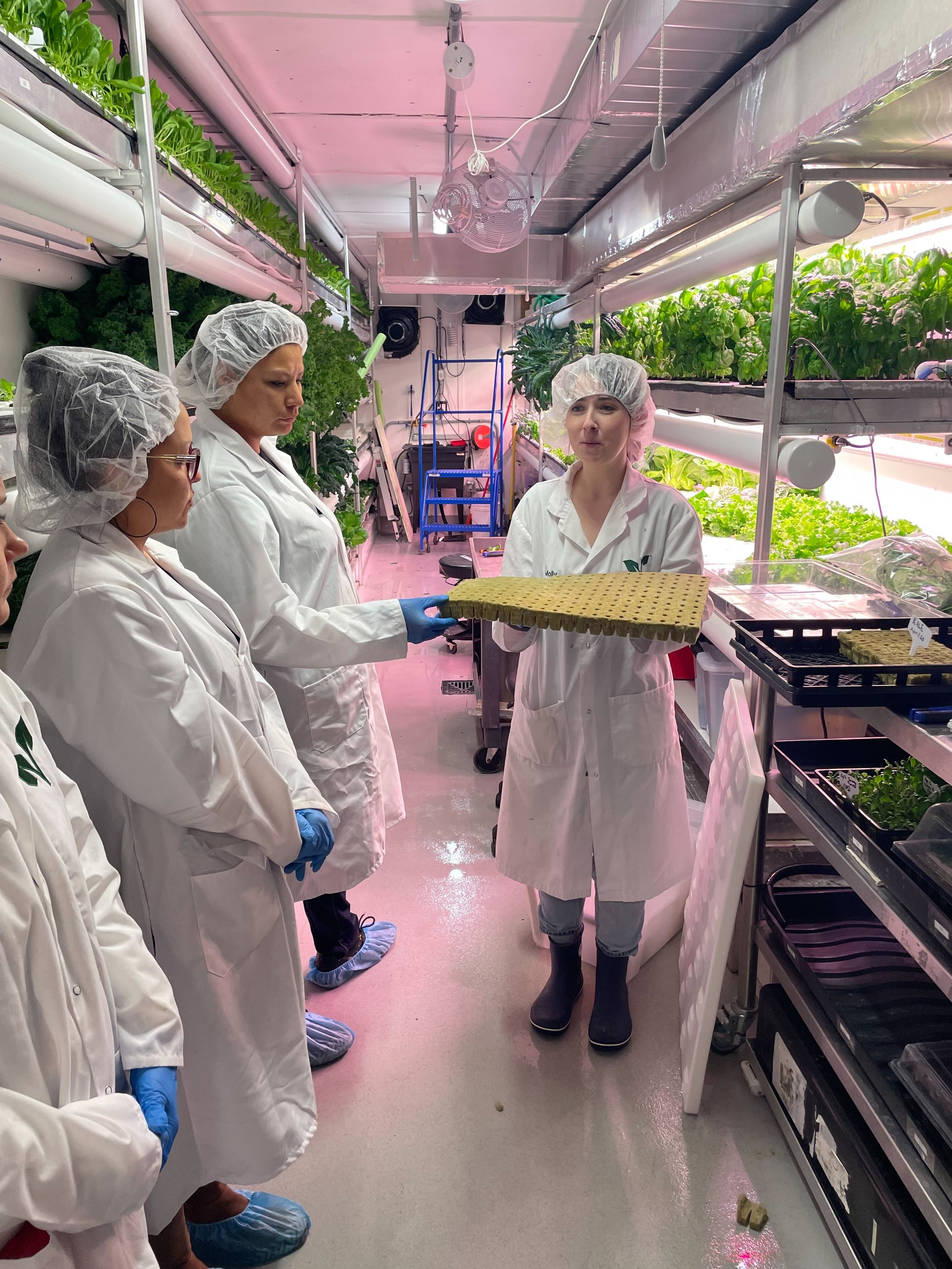
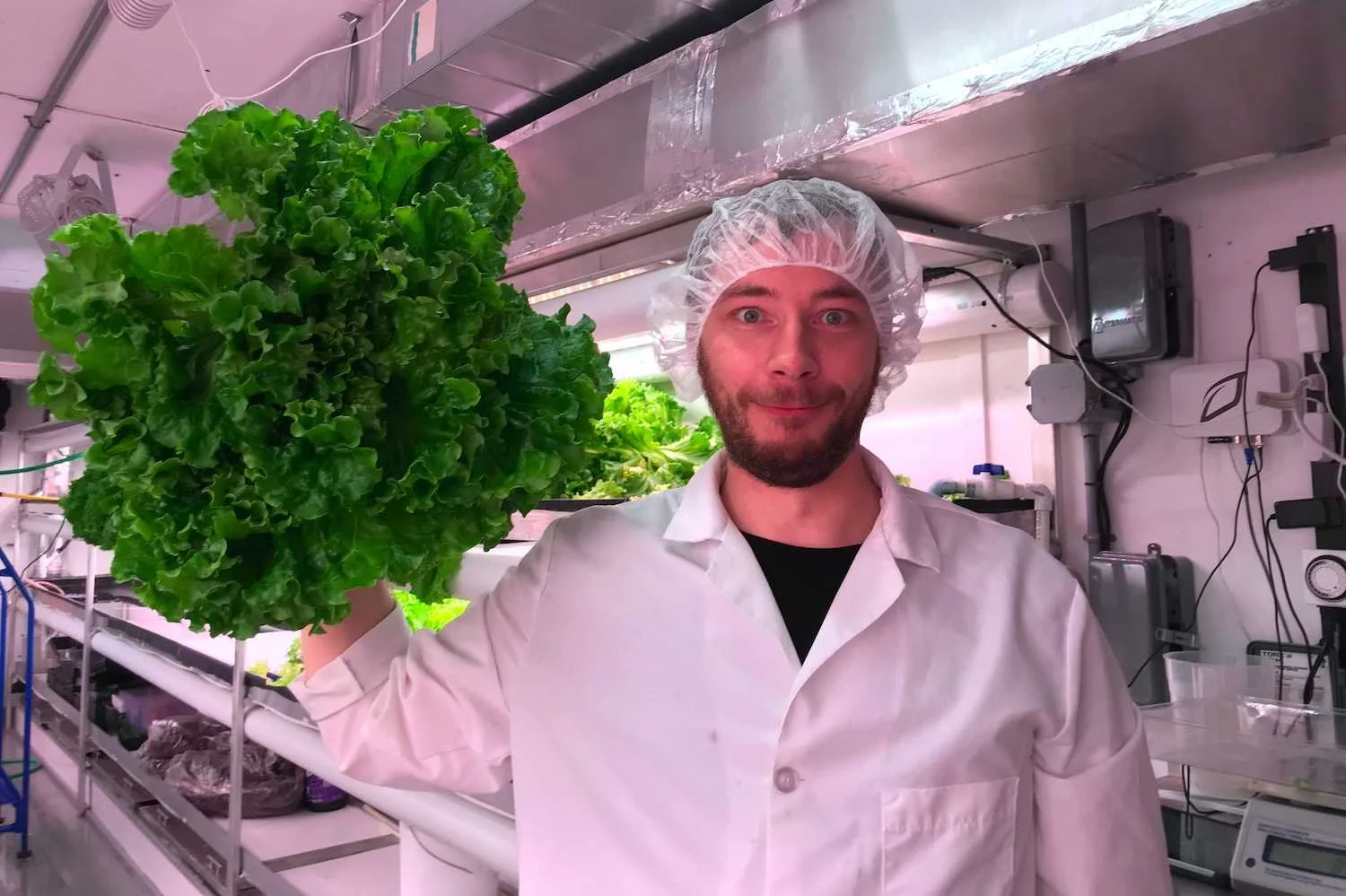
Lettuce shortage? Not here!
The R&D farm is an extension of our customers’ farms.
For example, say a customer wants to test out baby spinach in their system but doesn’t want to risk failure. Growcer’s R&D team, consisting of bonafide scientists (Ph.Ds!), conducts research experiments and passes along the conclusions to our customers.
Plus, Growcer’s R&D team uses the same modular farms our customers use. We follow the same standard operating procedures we ask of our customers, and are constantly validating if they are still the best practices within our farms
This means we can guarantee grower success from day one.
Growcer’s goal is to make year-round farming accessible to all, and that means averaging out the good AND bad yields to come up with a realistic number we know our customers can meet and sustain.
Our yield benchmarks are verified over hundreds of rounds of cultivation and we know with certainty that our customers can reach them because we’ve already accounted for varying conditions. Our yield benchmarks are not projections but a number you can count on. In fact, most customers meet and exceed our marketed yields.
It’s the same as opting for the tried-and-tested Toyota over a less proven, less reliable option. The difference reveals itself over time.