Research Summary: How many hours does it take to operate a vertical farm?
From seeding to maintenance, how many hours per week does it really take to grow produce year-round?
When we got down to timing individual tasks with a good old fashioned stopwatch, we used a diverse team with varying degrees of horticulture experience to mimic customers of all experiences.

The Why
Those of us in the vertical farming industry know that labour is one of the largest operating expenses. While there are fancy robots being made to make harvesting more efficient, there are still short term solutions that can help reduce labour hours in the meantime.
Growcer’s R&D team needed to quantify: How many hours does it actually take to grow year-round in a Growcer farm?
With a benchmark of hours, we could better understand
Where can we save time?
Are there any tasks we can do more efficiently?
Does it take more or less time than what we communicate (25-30 hours/week)?
The What
We used two models to calculate the work required to operate one of our farms:
The “Annual” model calculates the annual, monthly, and weekly predicted labour requirements for a farm growing a single crop type (for example, only lettuce).
The “Raft” model calculates the incremental addition of labour required for adding one raft of a specific crop into our farm. This model allows for a customized production schedule (who only wants lettuce?) and a better understanding of the labour required for our standard crop mix (most customers choose to grow 5 to 6 different varieties in their farms).
Each model has fixed and variable labour tasks.
Fixed tasks: Tasks that occur irrespective of the number of rafts in the farm. An example would be weekly system maintenance, like calibrating sensors.
Variable tasks: Tasks that scale with the number of rafts, and are further estimated based on the required output. An example would be packaging time required for a crop based on its projected yields.
We broke our model down into 5 main tasks, each with a number of sub-tasks to accurately reflect daily system operation. It is the equivalent of breaking down your work day based on every action - from typing an email to making a phone call.
When we got down to timing individual tasks with a good old fashioned stopwatch, we used a diverse team with varying degrees of horticulture experience.
This is important because we know our customers range from green thumb enthusiasts to people with farming experience. Having a diverse team for our labour timing trials ensures we have accurate representation of how much time it will take. Plus, it gives us more confidence when communicating with customers of all skill levels

5 main farming tasks used in the model
Production: includes seeding preparation activities, crop-specific seeding and density-specific transplanting
Harvest: includes crop- and density-specific production activities such as topping (for basil), “cut and come again” trims (for leafy greens and herbs) and complete harvests for all crops
Packaging: includes the weighing, packaging and labeling of a unit of produce based on projected yields. Specifically loose-leaf lettuce, leafy greens and herbs were packaged as grams per unit while choys and head lettuces were packaged as the number of heads
Maintenance: includes all system and equipment cleaning tasks, calibration of pH and EC sensors, refilling of water reservoirs, adding nutrients and stabilizing pH, as well as labeling of newly seeded crops
Plant Health: includes full system crop inspections and Integrated Pest Management (IPM) activities
Results
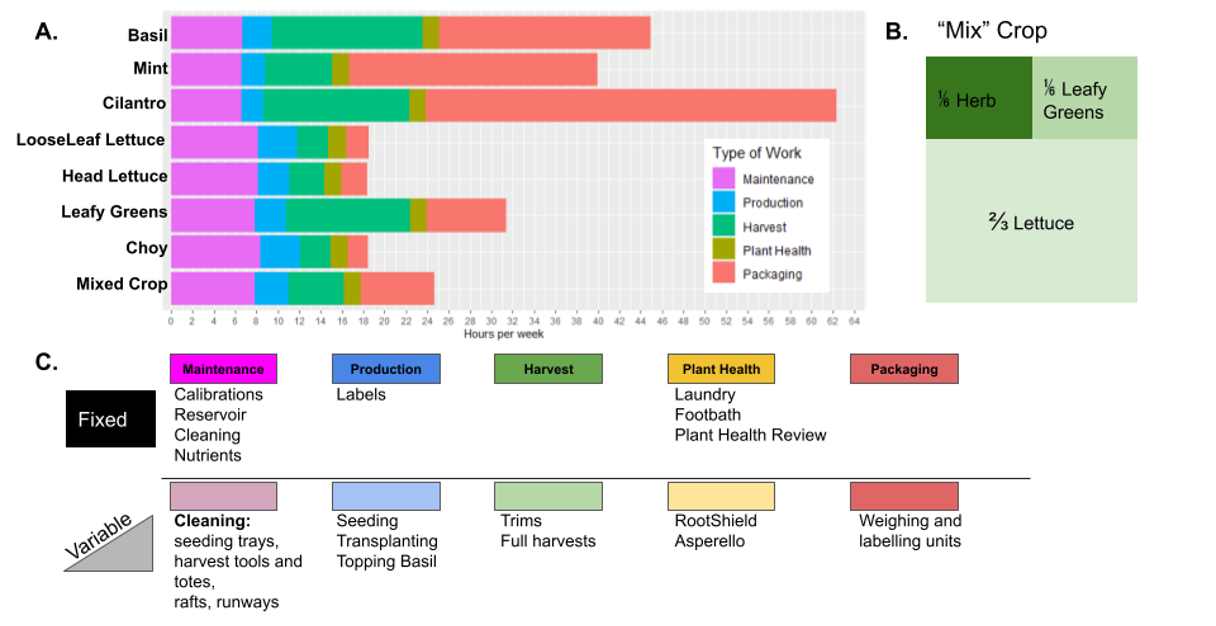
The following is the annual model design and results. Panel A represents the annual model estimates of the weekly labour necessary to operate our system with a single crop type. Panel B represents the division of crop types for a mixed crop operation and this mix was used to estimate weekly labour necessary when growing a mixed crop (the final bar in Panel A). You’ll see that while a mixed crop averages around ~25 hours per week, it is still less than if you were to grow 100% cilantro or basil which are herbs that require partial harvests and smaller packaging. Growing only lettuce requires the least amount of hours per week at an average of ~18. Panel C represents the overview of tasks and whether or not they were fixed or variable.
The labour required to grow different crops across all 5 task categories is different. We found herbs and leafy greens require the most labour while choys (bok choy, win-win choi) and lettuces required the least labour.
In a mixed crop setting (the most popular among customers), we confirmed it takes 24.6 hours/week to operate a Growcer farm at capacity assuming the customer is following all our Standard Operating Procedures (SOPs).
Depending on the mix of crops, extra help is beneficial on harvest and packaging days.
Also, your distribution channel matters. The ability to sell produce in bulk will drastically reduce your weekly labour requirements.
There is a strong connection between plant structure and harvest and packaging times.
For example, the shape of cilantro makes it more time consuming to harvest and package because the stems and leaves easily get tangled and require extra care on behalf of the operator to not cause damage.
This is notable for other cut-and-come-again harvests where you only remove part of the plant and have to make sure not to damage what is left growing.
If you are looking to cut back on labour hours, there is potential to reduce the frequency of these activities to save yourself time. (See point #1 - what you grow impacts how much time you spend in your farm!)
If spinach bolts, it greatly increases the harvest time. When spinach bolts it produces more, but smaller, leaves which need to be removed from the elongated (bolted) stem. See research on which spinach varieties are less prone to bolting here. Learning this provides opportunities for improvement in spinach’s growth schedule (baby spinach anyone?).
During the labour trials, we discovered opportunities for improvement in our current harvest and packaging procedures. Further improvements include combining these tasks into a single handling task to decrease potential damage from over-handling (taking a crop straight from the growing raft to package).
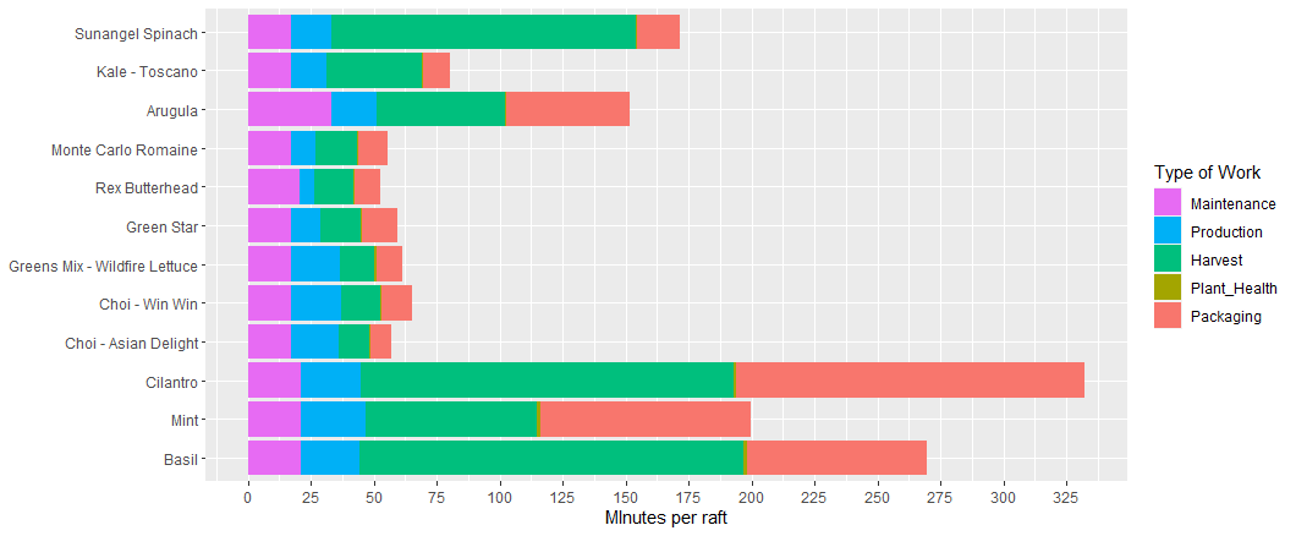
The Raft Model summarized results. The raft model estimates the additional labour needed per raft of a particular crop grown in the farm. Many rafts = more minutes, but you can see that harvesting or packaging are the biggest variable tasks across crop varieties.
So what? The conclusion.
What you grow impacts how much time you spend in your farm, because maintenance hours are consistent across crops but harvesting and packaging times are not.
What you grow impacts how much time you spend in your farm. If you are growing many crops, consider the fact that herbs and leafy greens require the most labour while choys (bok choy, win-win choi) and lettuces require the least labour.
On average, one person growing a full mixed crop production and following our standard operating procedures (SOPs) can expect to spend 25 hours in the Growcer farm per week.
However, we always recommend having at least two operators trained so you have extra help on harvest days or the option to take a vacation and have a back up!
Healthy plants require less of your time in the long run. For example, you will spend more time harvesting bolted spinach than unbolted spinach. Staying on top of daily maintenance pays dividends in the long run.
Also, your distribution channel matters. The ability to sell produce in bulk will drastically reduce your weekly labour requirements.
Make your life easy - invest in power tools to help with cleaning rafts or enlist the help of volunteers on harvest days (you can promise them some harvest leftovers) to cut back on labour time.
<img src="https://images.squarespace-cdn.com/content/v1/6348395313c2ab7c10565062/1686324392174-9N5LH7JXWL9ABS4TZYXZ/James_cleaning_Growcerfarm+copy.jpg" alt="James_cleaning_Growcerfarm copy.jpg" />
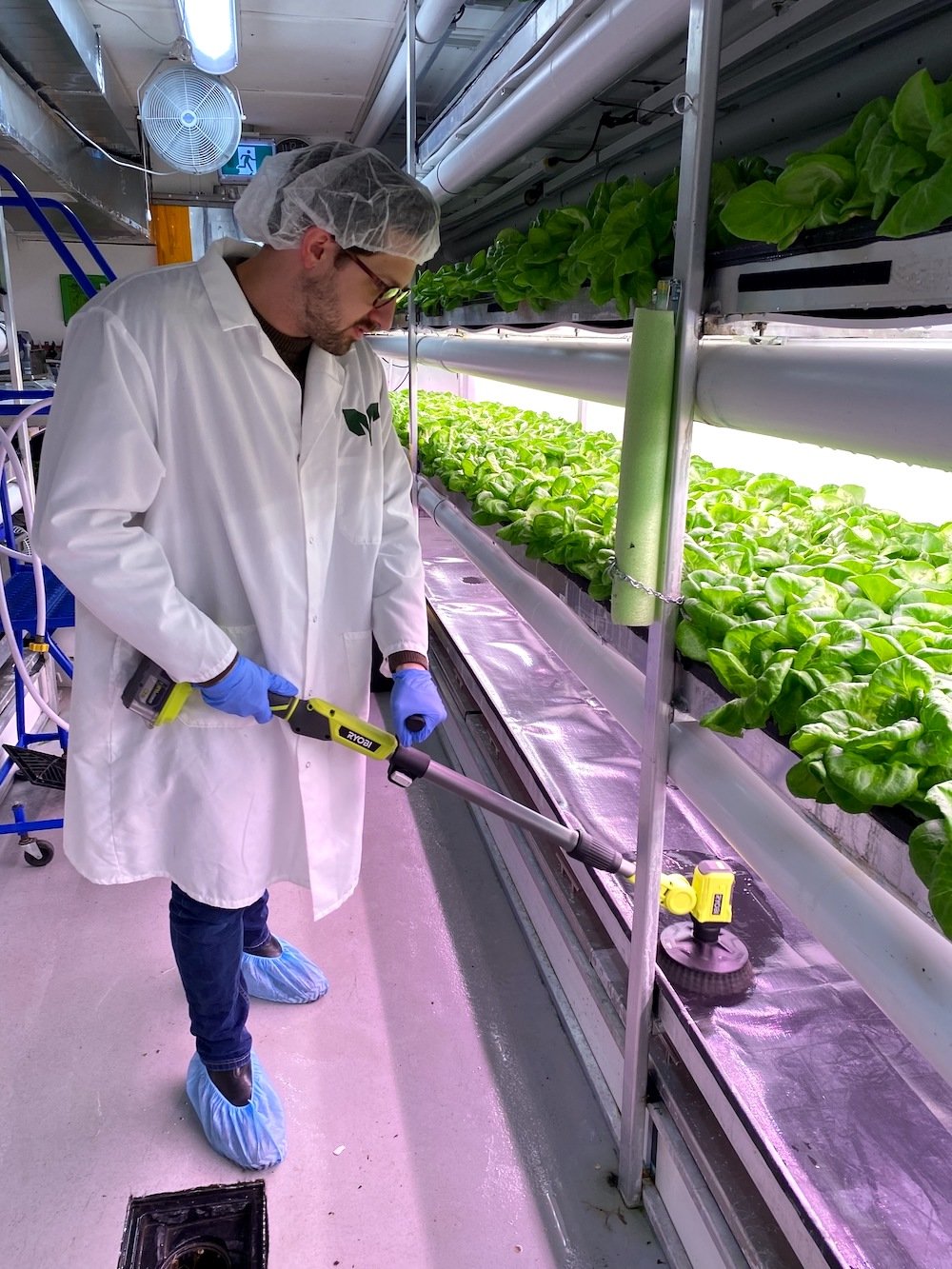
<img src="https://images.squarespace-cdn.com/content/v1/6348395313c2ab7c10565062/1686324392204-FAVQHE3DD9RZ5G3P1ORB/Katya_cleaning_Growcerfarm+copy.jpg" alt="Katya_cleaning_Growcerfarm copy.jpg" />
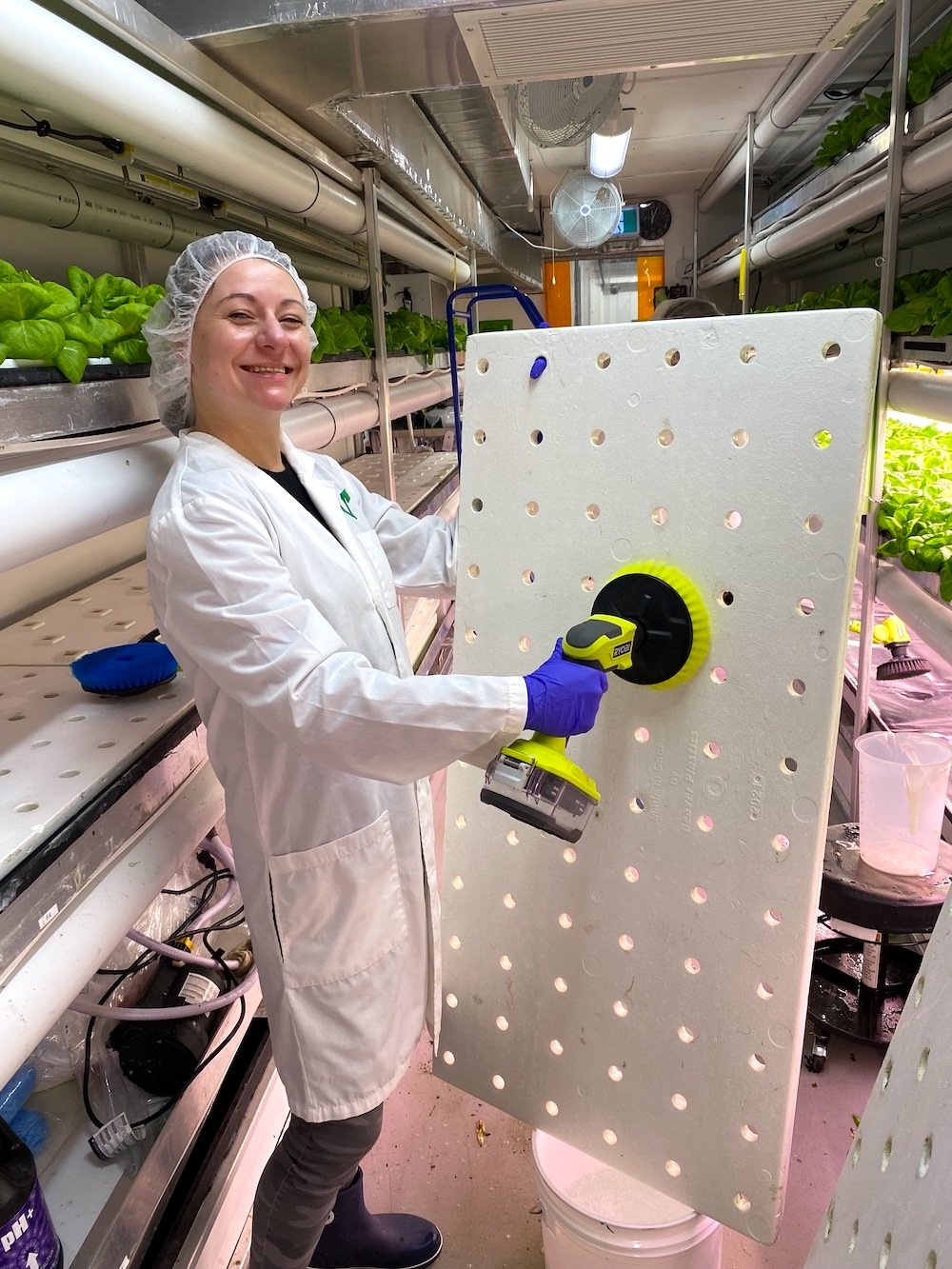
<img src="https://images.squarespace-cdn.com/content/v1/6348395313c2ab7c10565062/1686324393076-K9AVJM42EBKDOOM8UPK1/Michael_cleaning_growcerfarm+copy.jpg" alt="Michael_cleaning_growcerfarm copy.jpg" />
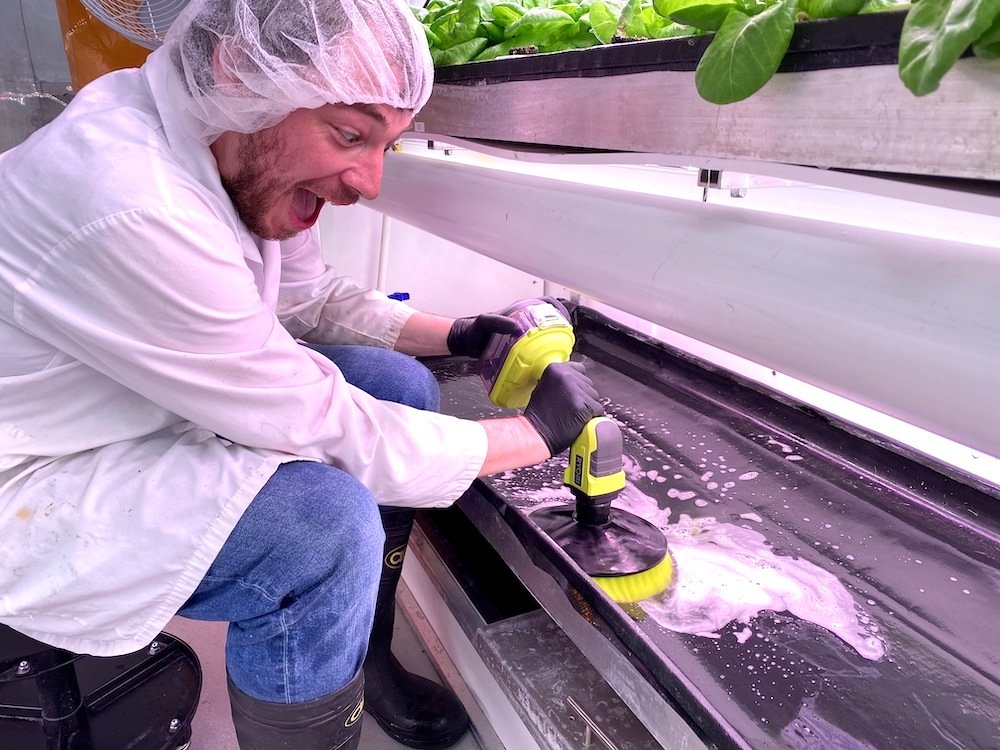
#block-yui_3_17_2_1_1686323783500_39620 .sqs-gallery-block-grid .sqs-gallery-design-grid { margin-right: -8px; }#block-yui_3_17_2_1_1686323783500_39620 .sqs-gallery-block-grid .sqs-gallery-design-grid-slide .margin-wrapper { margin-right: 8px; margin-bottom: 8px; }
Want to learn more or check out each phase of the trials? Connect with our research team.
Keep up with the latest trends, research, and all-around fresh takes by subscribing to our industry newsletter, STACKED.